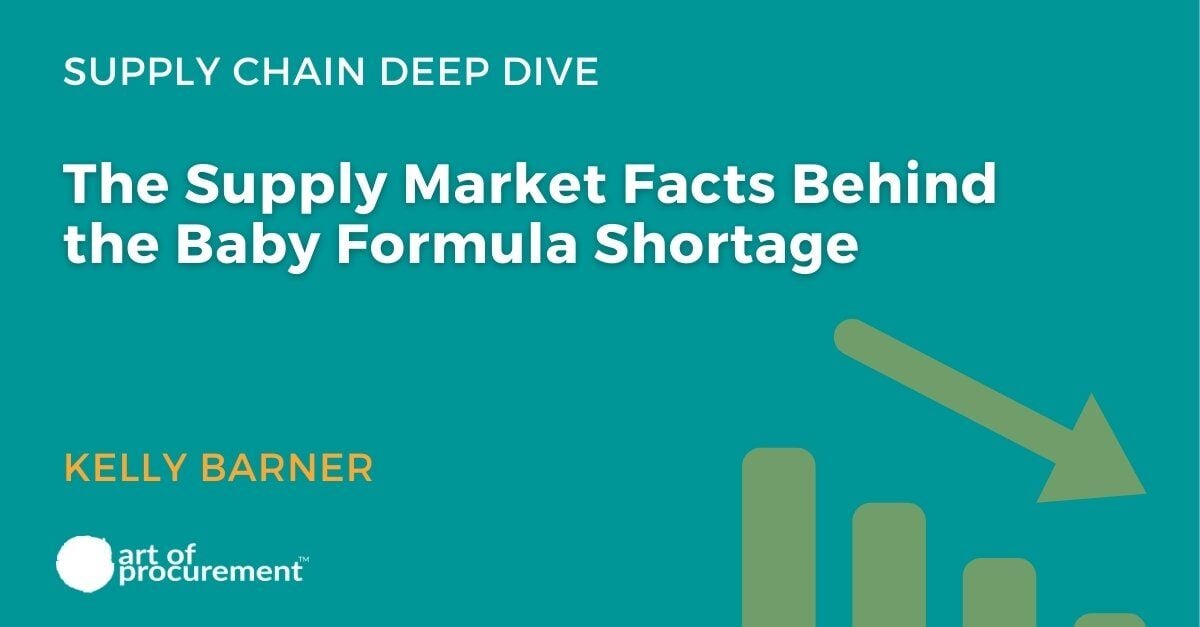
By now, supply chain professionals are used to our field being in the news. The latest drama: baby formula. Parents all over the country are scrambling to get their hands on the product they need to feed their children, and more than a few people have asked, where did the baby formula go?
I recently researched this story for an episode of Dial P for Procurement (you can listen to it here), but given all the relevant details and facts, it bears repeating in written form. Note: There are many serious allegations associated with this story, and we are not here to debate those – only to discuss the publicly available information related to the product shortage.
This is a multi-part story, and it is far more complex than even the loudest headlines suggest. Starting with over-concentration among U.S. based producers.
Who makes baby formula?
Just four domestic producers make up 89% of the U.S. market:
- Abbott Labs / Similac (43%)
- Reckitt Benckiser / Enfamil (37%)
- Nestle / Gerber
- Perrigo / Private Label
In 2020, parents started hoarding formula like the rest of us were stocking up on toilet paper. There weren’t necessarily any reported problems, but formula is something they didn’t want to be stuck without. As a result, demand eased in 2021 producers pulled back their production.
U.S. births increased in 2021 for the first time since 2014, and while it was only a 1% increase, more of those mothers are turning to formula to feed their babies. We’re coming off recessed production and demand is on its way up.
Tracking Out of Stock Rates
November 2021 is the month that out-of-stock rates first ticked above the 10% rate associated with elevated concern about formula supply. Out-of-stock percentages are measured by SKU. 40-45% of SKUs are out of stock, not 40% of baby formula by volume. This is important because, as with any product, there are a few SKUs that run right down the middle of the road, the common case.
Many of the stories making headlines are about infants with special nutritional or digestive needs. They might have an illness that requires them to have a specific type of formula. If out of stock rates are based on SKU, as in rows on retail shelves, there is a lot less product out there than 40-45% might suggest.
Here are the month-by-month rates according to the tracking site Datasembly:
- November: 11% out-of-stock
- December: 15%
- January: 20%
- February: mid 20’s%
- March: 30%
- As of April 24th, baby formula was running average out of stock rates of between 40-45% in most states.
As bad as 40-45% out-of-stock is, Iowa, South Dakota, North Dakota, Missouri, Texas, and Tennessee are showing out of stock rates over 50%.
Critical Tipping Point: The Formula Plant Closure
One plant in Sturgis, Michigan produces an enormous percentage of the formula used in the U.S. And while the closure has been highly publicized and blamed for driving the shortage, we are looking at the data. There was a problem months before that plant went down and recalls were issued.
To understand the plant closure, we have to look back to September of 2019. The regularly scheduled FDA inspection of the Sturgis, Michigan plant noted that Abbott was not testing a representative sample of the product at the final stage before distribution to discover quality issues. Then the COVID-19 pandemic hit, and all inspections came to a screeching halt.
Abbott went a full two years from September of 2019 to September of 2021 before there was a subsequent inspection, even though there was that quality testing issue documented by the FDA. When the FDA arrived in September of 2021 to do their inspection, they uncovered unsanitary conditions.
The FDA filed their inspection report, but not a lot happened publicly. It wasn’t until October of 2021 that a whistleblower came forward with allegations of lax cleaning practices, falsifying records, and information being concealed from the FDA. Investigations are ongoing, but the whistleblower spurred the FDA and Abbott to act. The Sturgis plant was closed in early March and the scope of the recall was increased to include more batches of product.
On May 16th, Abbott announced that they had entered into a “consent decree” with the FDA to reopen the plant. It will take two weeks to bring the plant back online, and then it will take six to eight more weeks for product to reappear on store shelves.
The attention around the formula shortage has reached a fevered pitch. But when news stories vaguely refer to “supply chain issues” they miss the mark. The truth is rarely simple, and I personally like specifics.
I went back through the Wall Street Journal month by month, looking for relevant stories. I didn’t go as far back as September 2019 because we know nothing was being reported publicly at that time. Instead, I went back to September of 2021, when we know the FDA inspection happened in advance of the whistleblower coming forward. This was also in advance of the out-of-stock rate hitting 11% and triggering public concern.
I did not find a news story about concerns over baby formula being out of stock until January 12th, 2022, in an article titled, Baby Formula Is Hard to Find, Brands and Stores Are Divided Over Why. There is no discussion of Sturgis plant. Instead, we read that retailers were blaming manufacturers and manufacturers were blaming retailers. The Infant Nutrition Council of America, an industry group representing baby formula manufacturers, blamed logistics providers and consumers.
Abbott talked publicly about intermittent, slow shipping and expected their issues to have improved quote in the coming months. That was a month prior to them closing the Sturgis plant. There was already a storm brewing.
Source of Market Concentration: Women, Infants, and Children
Even beyond the FDA’s inspections, the federal government is heavily involved in infant formula. WIC is the Women, Infants, and Children assistance program. WIC is federally funded but administered at the state level – and: 60% of all U.S. baby formula is bought through the WIC program, run by the Department of Agriculture.
Each state individually bids out the contract for their entire WIC voucher volume. Once the contract is signed, vouchers specify brand and container size. Abbott, the maker of Similac, is currently the supplier for over half of the agencies administering WIC. If 60% of all formula purchased in the U.S. is associated with the WIC program, half of that volume comes from Abbott.
The Biden administration has called for states to loosen their requirements. If a voucher says you are entitled to X ounces of Similac, but the store only has Enfamil, they’re trying to work out a way for that to happen. That said, these are legally binding contracts, and we know how quickly contracts are changed.
Unfortunately, all of this has led to panic buying, hoarding, and – worst of all – price gouging. A 12.5-ounce container of formula makes about 15 bottles depending on the age and size of the infant. That’s just a few days.
And we can’t ignore the effect of inflation. The average cost of the most popular baby formula is up by about 18% over the last 12 months.
Right after entering office, the Biden administration ordered a 100-Day review of supply chains. The initial report was released in June of 2021, 5 months before the out-of-stock rate started to tick upwards to 11%. There is no mention of baby formula in that initial report. On March 9th, 2022, sectoral assessments were released, including the USDA Agricultural Commodities and Food Products Ecosystem Report. There was also no mention of formula there.
In fact, in that report, the only mention of infants was a discussion of the WIC farmer’s market initiative. Formula was still not on the radar screen from the federal government’s perspective.
How is the market responding?
The most typical baby formula ingredients are dehydrated cows’ milk, vitamins, and sugar. These are simple products, but they must be available in the right quantity and at the right quality to be fed to infants.
Some news articles did mention packaging. Perhaps the ingredients are available to make the formula, but the liner for the jar or the lid or the seal or the label isn’t available, and those shortages are holding up production.
Labor shortages continue to be an issue and that can affect multiple points in the supply chain.
Enfamil, the primary competitor to Similac, saw an 18% surge in demand as parents started switching away from Similac. Abbot is currently shipping inventory in, from their FDA cleared plant in Ireland and they’re trying to increase production at a second facility in Ohio.
Perrigo, the private label producer for Walmart and Target, has stated publicly that they expect the shortages to last through the rest of 2022. Enfamil is increasing production as much as they can, but they’ve already been dealing with the surge.
In April, chains like Walgreens, CVS, and Target started putting limits on how many baby formula products consumers could purchase at a time. One of the retailers specifically mentioned that they did so at the request of the FDA. The FDA reportedly asked them to ration product to five containers per customer per day. Many retailers ratcheted this down further, limiting purchases to three containers per customer.
Update: Operation Fly Formula
Starting last week, U.S. military planes brought baby formula back to the U.S. from approved plants in Europe. A total of 1.5 million 8-ounce bottles of formula are expected to arrive throughout the week.
Of course, there is no simple fix for a complex problem. That formula is not headed for store shelves. It will be distributed to hospitals, doctors’ offices, healthcare facilities, and pharmacies where the government determines the need is most acute. Consumers outside of those areas will have to continue to scramble to find the formula they need to feed their infants.
What lesson should procurement learn from this?
This is an acute and cautionary tale that has been coming for years, resulting from the over concentration of markets.
We talk about this dynamic in procurement all the time. In the past, all that mattered was leveraging the maximum volume to drive down prices as much as possible. That led to concentration in a lot of markets because companies and suppliers were looking for efficiencies of scale.
Once you have a supplier that represents 43% of national production, you have a critical item, and you are basically asking for trouble. We should have expected supply chain failure.
Clearly, we need to rethink our notions of essential products.
We need to be aware of the intent behind quality testing. We need to take a broader perspective on what should be produced by how many companies.
Looking at this from a corporate standpoint, how much of a company’s demand do we want dependent on one supplier at the first tier, let alone the second tier and beyond. And yet the government does not hold the answer – they failed to prevent the need for a plant shutdown and recall and were slow to respond in the face of critical shortages.
Whether we work in supply chain, procurement, retail, manufacturing, or distribution, there are lessons we need to learn from what has happened here.