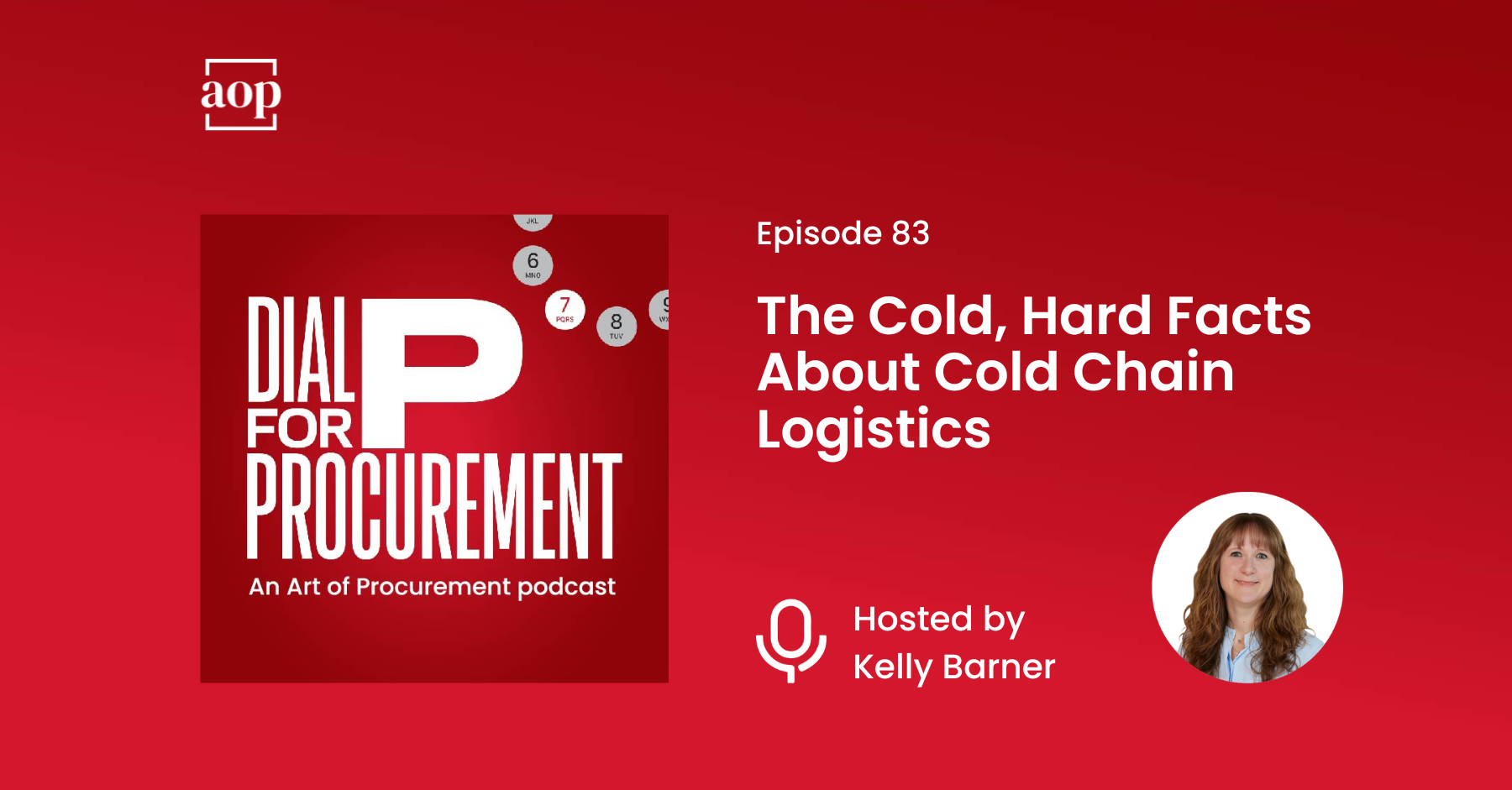
The term “cold chain” was first used in 1908 to describe meat industry storage and transportation in and out of St. Katharine Docks in London. In just three years, available cold capacity exploded from 59,000 units to 2.84 million. As revolutionary as it was for the time, St. Katharine Docks was still dependent on ice for cooling.
It would be 30 years before a more modern source of portable refrigeration became available. In 1938, Frederick McKinley Jones and Joe Numero founded ThermoKing. They designed a portable air-cooling unit for trucks carrying perishable food and patented it in 1940. Once again, it was innovative and impactful, but the cold chain was still just scratching the surface in terms of the potential for long distance low temperature logistics.
How cold is cold?
Today there are multiple ways to keep shipments cold. Mechanical refrigeration or “reefer” trucks provide one option, and thermal containers with dry ice in them are another. To be truly seamless, insulated containers with dry ice in them allow products to move through the supply chain with minimal variability regardless of stops, distance, or external conditions. Shippers simply calculate the amount of dry ice required for the expected number of days and pack the containers in advance. Then they hope everything goes as planned.
Many transported products require refrigeration, but they don’t all need to be the same level of cold, and they don’t all face the same risk should conditions fall outside of their ideal temperature range. For instance, perishable food and flowers can be moved and stored at very different temperature ranges than frozen food and sensitive pharmaceuticals.
As a result, there is more than one temperature range in the cold chain:
- Common range is 36 to 46 °F (2 to 8 °C)
- Frozen chain requires -4° F (-20° C)
- Ultralow or ultracold requires -94° F (-70 °C)
The cold chain clearly predated COVID by over a century, but the transportation needs of the COVID vaccines kicked development, monitoring, and innovation into overdrive because some of the COVID vaccines required ultracold transportation and specialized packaging.
In fact, dry ice was the only way to keep the Pfizer vaccine cold enough: -94 °F / -70 °C. By comparison, Moderna’s vaccine was stable at 2-8 °C, the common cold chain range, for up to 30 days, and it could be outside of cold storage for longer. That paid dividends at injection facilities and in doctor’s offices.
Only 25-30 countries in the world have the infrastructure required for the ultracold cold chain. This infrastructure includes vehicles, airports, and distribution centers, but it also includes the moves between them. The cold chain is a high-tech modern marvel in more than one way – but it doesn’t come cheap.
Costly Cold Chains
Supply chain professionals are used to technological innovation, some of which has to do with the mechanics of our work. But new capabilities are also derived from tracking, monitoring, and reporting. They may be less glamorous, but they are no less critical to the viability of a profitable, sustainable cold chain.
Think about the many forms of cost that may be associated with a ruined shipment: money, time, lives, and brand damage. A lot is riding on the logistics provider’s ability to get the product safely to its destination.
Every player in the supply chain has to meet condition expectations and prove that those conditions were maintained every step of the way. Often this is done through centralized monitoring and integrated telematics, which uses GPS tracking devices to provide near real time monitoring of the key metrics for a given shipment.
If conditions move outside of the tolerated range, it is possible to communicate with the driver immediately – hopefully in time to save the shipment.
Like many other operational processes, cold chain logistics creates a mountain of data for monitoring and optimization. Any equipment movement or status change that could affect the product is tracked. That includes the movement of truck or shipping container doors, weather events, and traffic delays.
Cold Case Example: Ozempic
Ozempic’s logistics requirements were recently featured in the Wall Street Journal, bringing cold chain logistics back into the news. Ozempic is a prescription injection used for treating Type 2 Diabetes and weight loss (under the product name Wegovy), and it has to be transported in the standard cold chain range, between 36 and 46 °F, to protect the effectiveness of its active ingredients.
The complicated and costly logistics associated with refrigerating these prescriptions is eating into manufacturer Novo Nordisk’s profit margins, and they are not alone.
AmerisourceBergen makes a comparable diabetes drug that also has to travel via the cold chain. CFO James Cleary has stated that the drugs are barely profitable from an operating income standpoint – because of the cost to transport them.
The spot rate for refrigerated trucks was $2.44 a mile in July compared with $2.07 a mile for dry vans, according to the most recent data from online freight marketplace DAT Solutions. That’s 18 percent more – a significant but necessary expense.
In 2020, everyone and their mother was riveted by what supply chains can do. That only increased when people discovered today’s cold chain capabilities and saw them roll into action to make the COVID vaccine widely available.
The cold chain has largely slipped from the headlines, but we shouldn’t take it for granted.
The race is on to meet demand for refrigerated fleet equipment and warehouse space, to reduce the risk at transition points, and to ensure constant conditions through a seamless chain of custody.
Doing that is expensive, which means that whether you work in procurement or supply chain, this topic may cross your desk. Be informed, be ready to consider all of the contractual obligations, but don’t forget to stop and be impressed as well.